The locking jaws should engage the kingpin at its base, where it begins to widen. This ensures a secure and stable connection between the trailer and the towing vehicle.
The interaction between the locking jaws and the kingpin is a critical aspect of trailer towing safety and efficiency. The design of the kingpin and the corresponding locking mechanism is engineered to provide a robust connection that can withstand the rigors of the road. This connection point is pivotal in distributing the towing forces evenly, minimizing wear and tear on both components, and ensuring the trailer’s stability during transport.
Regular maintenance and inspection of the kingpin and locking jaws are essential for safe towing practices. Operators should check for signs of wear, proper engagement, and correct pressure application to prevent disconnection or failure. The use of high-quality materials in the construction of both the kingpin and the locking jaws contributes to the longevity and reliability of the towing setup.
Innovations in hitch design, including adjustable locking mechanisms and enhanced safety features, continue to improve the ease of use and security of trailer towing. The importance of this connection and adhering to best practices in maintenance and operation can significantly reduce the risk of accidents and ensure a smooth towing experience.
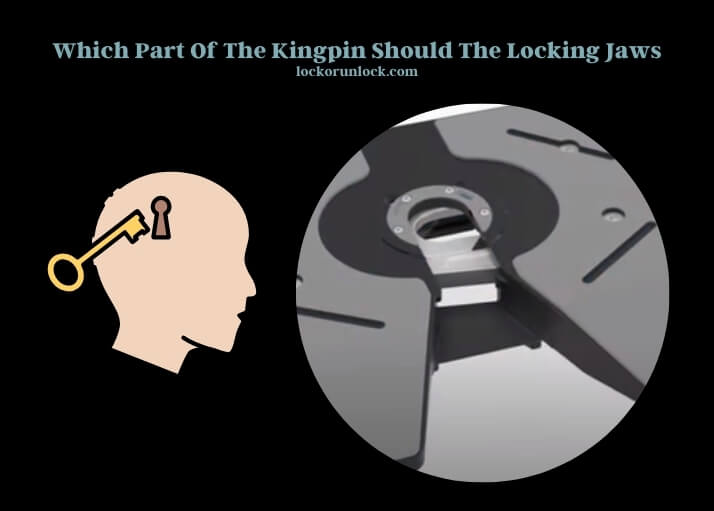
Secure Attachment: Locking Jaws Meeting the Kingpin
The interaction between the locking jaws and the kingpin is fundamental to the safety and stability of a towing setup. The locking jaws are designed to encircle the kingpin, which is a protruding pin from the trailer’s underside, to create a secure connection between the trailer and the towing vehicle. This connection is pivotal for the distribution of weight and the stability of the trailer while in motion.
The design principles of hitch systems focus on ensuring that this connection can withstand the dynamic forces encountered during towing. Safety mechanisms are integrated to prevent accidental detachment, and towing stability is enhanced through precise engineering of the locking mechanism.
The effectiveness of this interaction relies heavily on the correct alignment and engagement of the locking jaws with the kingpin, ensuring that the trailer remains securely attached under various driving conditions.
Durability and Design: The Backbone of Locking Jaws
Materials play a crucial role in the durability and functionality of locking jaws. The choice of material affects not only the longevity of the hitch system but also its performance under stress. Steel, alloy, and composite materials are commonly used, each offering different benefits in terms of strength, corrosion resistance, and weight.
Material Durability and Corrosion Resistance
Material Type | Durability Rating | Corrosion Resistance |
Steel | High | Moderate |
Alloy | Very High | High |
Composite | Moderate | High |
Innovations in design further enhance the durability of locking jaws. Engineers strive to create mechanisms that are not only strong but also resistant to wear and environmental factors. The integration of advanced materials and design innovations ensures that locking jaws can provide a reliable connection over an extended period, even under harsh towing conditions.
Maintenance: Key to Optimal Performance
Regular maintenance is essential for optimizing the performance of locking jaws. A well-maintained hitch system is less likely to encounter failures or performance issues. Maintenance routines should include inspections for wear and damage, lubrication of moving parts, and adjustments to ensure proper alignment and engagement.
Adhering to a maintenance schedule and following best practices can prevent common issues such as jamming, corrosion, and improper locking. Troubleshooting common problems promptly ensures the longevity and reliability of the towing setup, maintaining safety and performance.
Safety Innovations: Advancing Tow Hitch Technology
Recent advancements in locking jaw mechanisms have significantly improved safety and ease of use. Innovations such as auto-locking systems and visual indicators provide users with confidence that the connection is secure.
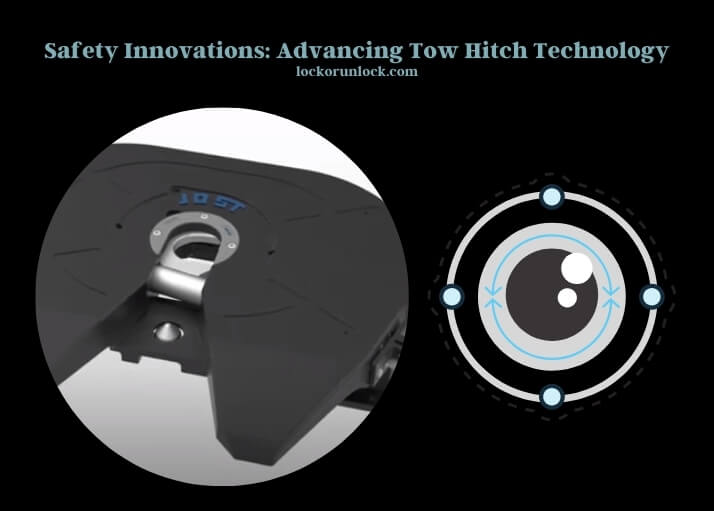
Advancements in Safety Features
Feature | Description | Benefit |
Auto-locking System | Automatically secures the kingpin | Increases safety, reduces setup time |
Visual Indicators | Provides visual confirmation of secure lock | Enhances user confidence, ensures proper attachment |
These technological advancements reflect the industry’s commitment to enhancing the safety of towing systems. Feedback from users has been instrumental in guiding these innovations, ensuring that they meet the practical needs of those who rely on towing for work and recreation.
Environmental Impact: Weather and Wear
The performance of locking jaws and their interaction with the kingpin can be affected by environmental conditions. Weather elements such as rain, snow, and extreme temperatures can contribute to wear and corrosion, potentially compromising the integrity of the connection.
Preventive measures, such as using corrosion-resistant materials and protective coatings, can mitigate these effects. Additionally, understanding the impact of environmental conditions on towing equipment can guide maintenance practices, ensuring that the system remains reliable in various climates.
Frequently Asked Questions (FAQs)
Optimal Contact Point for Locking Jaws on the Kingpin
Identifying the precise location on the kingpin where the locking jaws should engage is crucial for towing safety. The locking jaws should clasp around the base of the kingpin, where it begins to widen. This area provides the most secure grip, ensuring that the trailer and towing vehicle remain firmly connected.
The design of the kingpin and locking jaws is such that this contact point maximizes the surface area for the lock, distributing the towing forces evenly and reducing the risk of disconnection or wear over time. Regular inspection of this engagement point is recommended to ensure the integrity of the connection remains uncompromised.
Importance of Correct Locking Jaw Pressure
The amount of pressure applied by the locking jaws on the kingpin is vital for a secure connection. Too little pressure and the risk of a disconnection increases; too much pressure, and there could be undue wear on both the kingpin and the jaws, leading to potential failure.
Manufacturers typically specify the optimal pressure settings, and it’s essential for operators to adhere to these guidelines. Adjusting the locking mechanism to achieve the correct pressure ensures a balance between a tight, secure connection and preserving the longevity of both the kingpin and the locking jaws.
Impact of Kingpin Wear on Locking Jaw Function
Over time, the kingpin can experience wear from regular use, which can affect how the locking jaws engage. Wear can reduce the diameter of the kingpin, compromising the secure fit of the locking jaws.
It’s important for operators to monitor the condition of the kingpin regularly and consider replacement if significant wear is detected. Using a worn kingpin not only jeopardizes the safety of the towing setup but can also increase the stress on the locking jaws, accelerating their wear and potentially leading to failure.
Adjusting Locking Jaws for Different Kingpin Sizes
While standard kingpin sizes are widely adopted in the industry, there can be slight variations in diameter or shape due to manufacturing differences or wear. It’s essential for the locking jaws to be adjustable to accommodate these variations, ensuring a secure fit regardless of minor differences.
Operators should be familiar with the adjustment process for their specific hitch system and make necessary adjustments whenever a new trailer is connected. This adaptability ensures that the locking mechanism can provide a secure connection across a range of kingpin sizes.
Role of Lubrication in Locking Jaw and Kingpin Interaction
Lubrication plays a critical role in the interaction between the locking jaws and the kingpin. Proper lubrication reduces friction, wear, and the risk of corrosion, ensuring smooth operation and extending the lifespan of both components.
Operators should follow the manufacturer’s recommendations for lubrication types and schedules. Regularly applying the correct lubricant not only facilitates a better connection but also makes it easier to engage and disengage the locking jaws, enhancing the overall usability of the towing setup.
Diagnosing and Fixing Locking Jaw Misalignment
Misalignment of the locking jaws can lead to improper engagement with the kingpin, posing a significant safety risk. Causes of misalignment can include incorrect installation, wear and tear, or damage from towing incidents. Diagnosing misalignment involves inspecting the locking mechanism for signs of uneven wear or difficulty in locking and unlocking.
Fixing misalignment typically requires realigning or replacing parts of the locking mechanism. In some cases, professional service may be necessary to ensure the locking jaws are correctly aligned and functioning safely. Regular checks for signs of misalignment can prevent towing accidents and ensure the longevity of the hitch system.
Summary
The secure attachment of the locking jaws to the kingpin is crucial for towing safety and stability. Material choice, regular maintenance, and technological innovations play significant roles in ensuring the durability and reliability of this connection. The impacts of environmental conditions, users can maintain optimal performance of their towing systems, ensuring a safe and secure towing experience.